Rotating detonation engines (RDEs) have been the subject of theory and speculation for decades, but have yet to cross from theory to practical application. But now, it looks as though these exotic propulsion systems are about to make the leap into operational platforms.
In theory, a rotating detonation engine promises to be much more efficient than traditional jet engines, potentially providing missile applications a serious boost in range and speed. That could also mean fielding smaller weapons capable of achieving the same speeds and ranges as today’s missiles.
In aircraft applications like jet fighters, rotating detonation engines could offer similar benefits to missiles in terms of range and speed while potentially reducing maintenance requirements. Fighters, in particular, rely on afterburners, which effectively firehose fuel into the engine’s exhaust stream for added thrust. This rapidly depletes fuel stores and reduces the fighter’s range. RDEs could potentially allow for a similar boost in thrust with a dramatically reduced fuel penalty.
But where this technology could be the most useful is in powering the Navy’s future non-nuclear surface vessels, providing increased power production, range, and speed while having a seriously beneficial impact on the Navy’s budgetary bottom line.
Related: The Air Force is eyeing groundbreaking new engines for the F-35
Harnessing the power of detonation
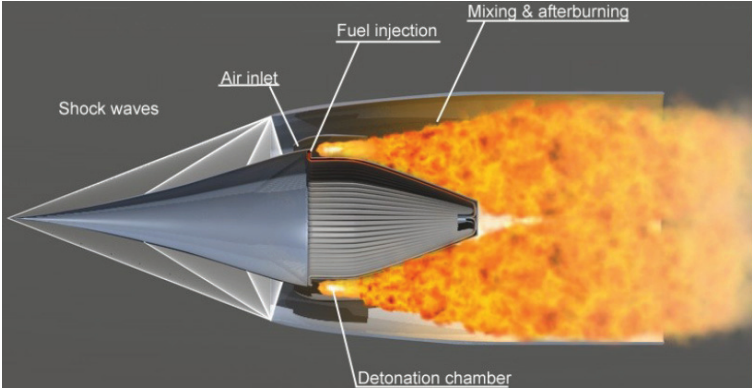
The concept behind rotating detonation engines dates back to the 1950s. In the United States, Arthur Nicholls, a professor emeritus of aerospace engineering at the University of Michigan, was among the first to attempt to develop a working RDE design.
In some ways, a Rotating Detonation Engine is an extension of the concept behind pulse detonation engines (PDEs), which are, in themselves, an extension of pulsejets. That might seem confusing (and maybe it is), but we’ll break it down.
Pulsejet engines work by mixing air and fuel within a combustion chamber and then igniting the mixture to fire out of a nozzle in rapid pulses, rather than under consistent combustion like you might find in other jet engines.
In pulsejet engines, as in nearly all combustion engines, igniting and burning the air/fuel mixture is called deflagration, which basically means heating a substance until it burns away rapidly, but at subsonic speeds.
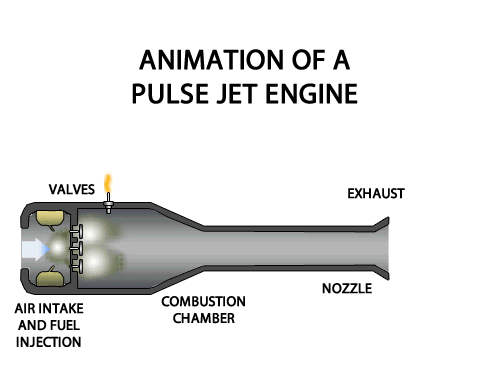
A pulse detonation engine works similarly, but instead of leveraging deflagration, it uses detonation. At a fundamental level, detonation is a lot like it sounds: an explosion.
While deflagration speaks to the ignition and subsonic burning of the air/fuel mixture, detonation is supersonic. When the air and fuel are mixed in a pulse detonation engine, they’re ignited, creating deflagration like in any other combustion engine. However, within the longer exhaust tube, a powerful pressure wave compresses the unburnt fuel ahead of the ignition, heating it above ignition temperature in what is known as the deflagration-to-detonation transition (DDT). In other words, rather than burning through the fuel rapidly, it detonates, producing more thrust from the same amount of fuel; an explosion, rather than a rapid burn.
“The detonation process is a more rapid and efficient extraction of energy from your fuel from a thermodynamic standpoint when compared to deflagration,” Dee Howard endowed professor of hypersonic and aerospace engineering, Dr. Chris Combs, told Sandboxx News.
The detonations still occur in pulses, like in a pulsejet, but a pulse detonation engine is capable of propelling a vehicle to higher speeds, believed to be around Mach 5. Because detonation releases more energy than deflagration, detonation engines are more efficient — producing more thrust with less fuel, allowing for lighter loads and greater ranges.
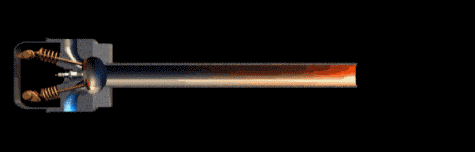
The detonation shockwave travels significantly faster than the deflagration wave leveraged by today’s jet engines, Trimble explained: up to 2,000 meters per second (4,475 miles per hour) compared to 10 meters per second from deflagration.
In May of 2008, the Air Force Research Laboratory made history by building the world’s first crewed pulse detonation-powered aircraft, using a Scaled Composites home-build plane called the Long-EZ. The unusual franken-plane managed a speed higher than 120 miles per hour during its test flight, with test pilot Pete Siebold at the stick, and reached altitudes between 60 and 100 feet.
“This is a potential game-changer in terms of fuel efficiency,” The AFRL’s Propulsion Directorate’s Fred Schauer said of the PDE powering Long-EZ.
“For comparison, if we had operated this same engine with conventional combustion we would have made less than a third of the thrust for the same fuel burn. In comparison to traditional engines, fuel savings of five to 20 percent could be expected.”
The Air Force assessed at the time that improvements to their PDE engine could eventually propel aircraft to speeds beyond Mach 4, and higher if combined with other advanced propulsion systems like scramjets. A rotating detonation engine could be even more effective, but many within the academic and engineering communities questioned whether such an engine could ever actually be built.
Related: US announces successful tests of 3 hypersonic missiles in 2 weeks
The Rotating Detonation Engine emerges
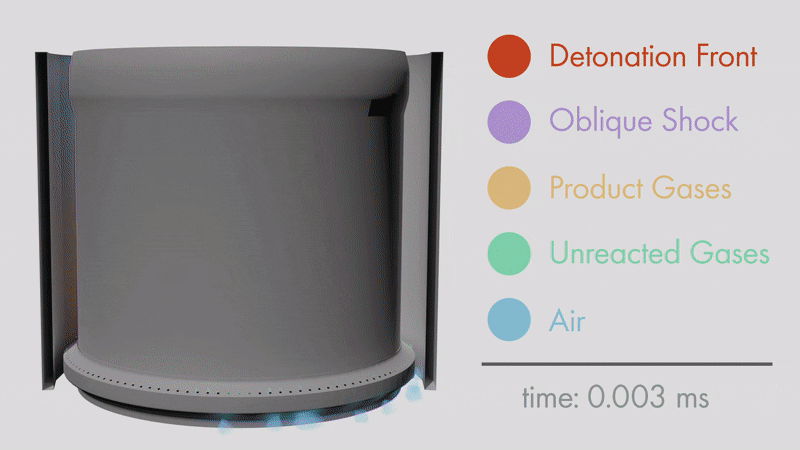
A rotating detonation engine takes this concept to the next level. Rather than having the detonation wave travel out the back of the aircraft as propulsion, it travels around a circular channel within the engine itself.
Fuel and oxidizers are added to the channel through small holes, which are then struck and ignited by the rapidly circling detonation wave. The result is an engine that produces continuous thrust, rather than thrust in pulses, while still offering the improved efficiency of a detonation engine. Many rotating detonation engines have more than one detonation wave circling the chamber at the same time.
As Aviation Week & Space Technology Defense Editor Steve Trimble explains, RDEs see pressure increase during detonation, whereas traditional jet engines see a total pressure loss during combustion, offering greater efficiency. In fact, rotating detonation engines are even more efficient than pulse detonation engines, which need the combustion chamber to be purged and refilled for each pulse.
“In theory, RDE is a bit like the leap from turbojets to turbofans in the 1960s, but for high-supersonic vehicles. It should give you a big jump in specific impulse (aka fuel efficiency), and if you can figure out how to package it in a way that doesn’t make things significantly heavier or less aerodynamic, you should be able to get a nice range boost out of it,” Trimble explained.
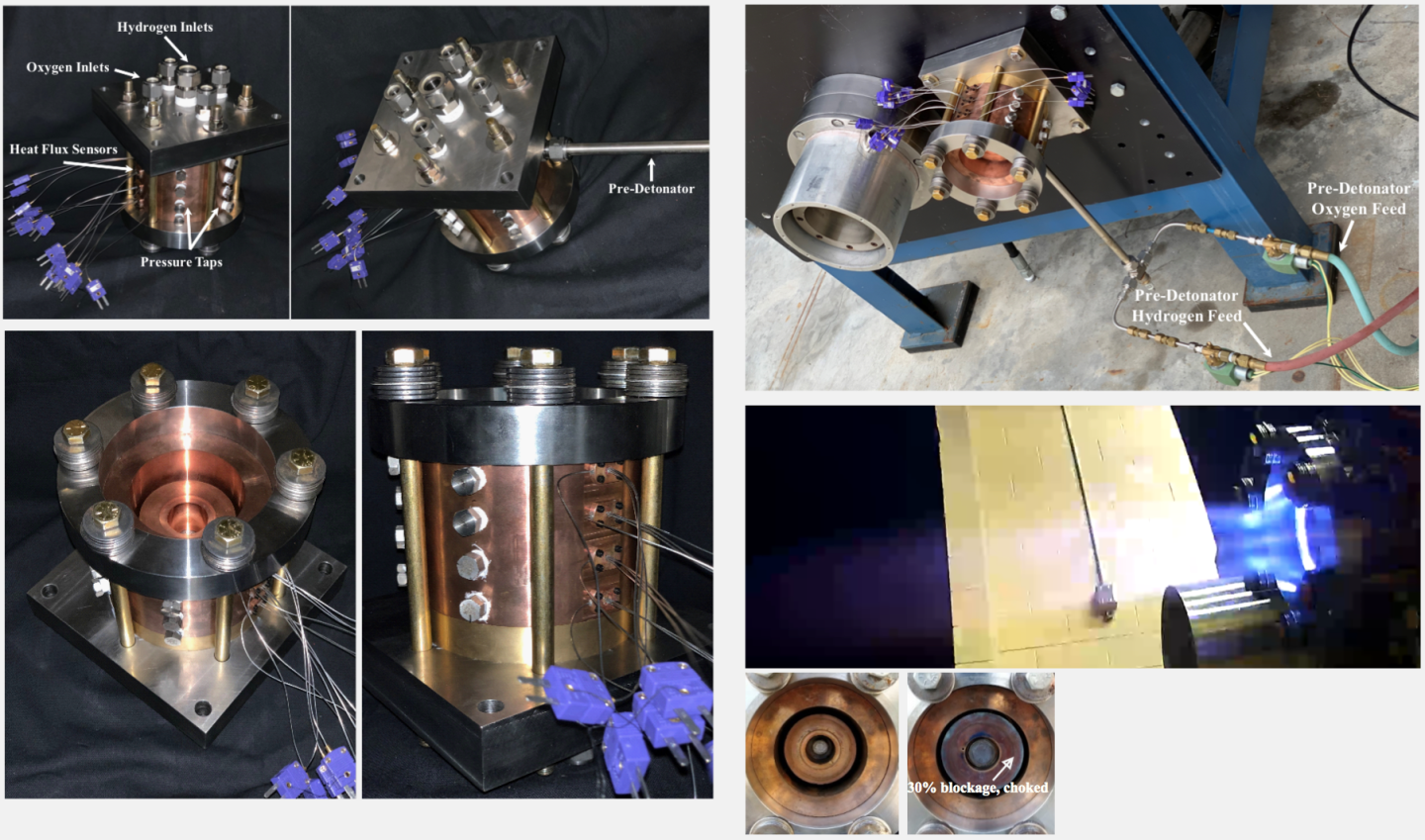
In 2020, a team out of the University of Central Florida, working with the Rotating Detonation Rocket Engine Program at the Air Force Research Laboratory, successfully built and tested the world’s first working rotating detonation engine that continued firing until its fuel was cut off, effectively proving the concept was possible. The three-inch copper test rig developed by the team successfully produced 200 pounds of thrust in laboratory conditions.
Since then, a number of other programs have followed suit, with noted engine manufacturer Pratt and Whitney among those leading the charge.
Read more from Sandboxx News
- The Air Force is eyeing groundbreaking new engines for the F-35
- GE’s new fighter engine just blew away existing jet technology
- The F-14 Tomcat’s biggest threat was its TF30 engines
- The Air Force wants air-breathing engines for hypersonic missiles
- DARPA’s new missile hints at truly game-changing technology